Determining whether to perform a test in-house or use contract testing is a key for all labs.
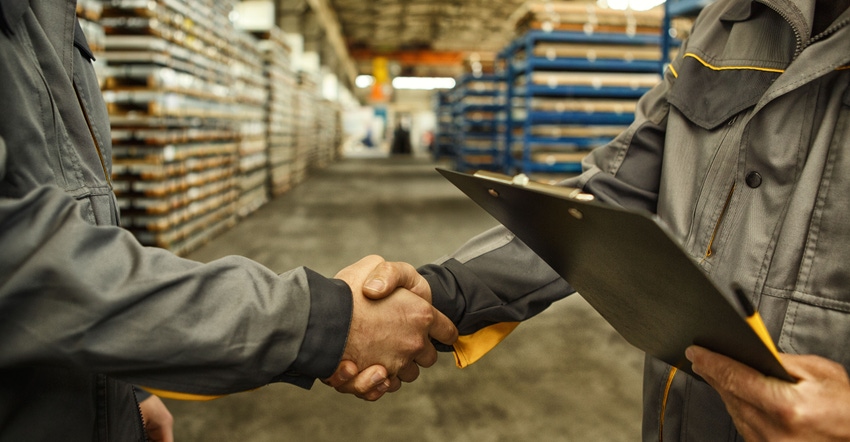
Whether to use in-house testing or contract testing is a choice that is specific to each supplement company and assay target. Considerable thought should be given to how in-house testing is used and how in-house labs are equipped. Those making these decisions should understand the company’s needs and the consequences of their choices. Some of the considerations used to make this determination should be frequency, turnaround, monetary cost, personnel, equipment, build-out, method development, method verification/validation, standards, standard operating procedures (SOPs) and out of specification (OOS) investigations.
Frequency
Knowing how often a test is needed is essential because that rate impacts the total cumulative cost for contract testing and the resources that are required for in-house testing. Prioritize the further evaluation of tests that have a higher cumulative cost to determine whether in-house testing is more cost-effective than contract. Identity testing of certain dietary ingredients fits well into this category because of the regulatory requirements for dietary supplements.
Turnaround
While it might be expected that in-house testing would be faster than contract, the ability of contract labs to process samples from multiple customers in batches can greatly increase their throughput. This could allow for a faster turnaround at the contract lab, although the cost may also increase due to rush fees. Certain strength assays that require unique instrument conditions (e.g., some high-performance liquid chromatography [HPLC] methods) might take longer for an in-house lab to report because the lab is concentrating on release testing of samples that can be batched together.
Cost
Identifying the monetary cost of a contract test is simple; most of that information is available on an invoice. Determining the cost of in-house tests that are batch-processed is also relatively easy because one estimate might suffice for all samples that are analyzed by that technique (e.g., residual solvents, heavy metals, pesticides and microbiological). More specialized assays (e.g., strength confirmation for botanical extracts) will require individual cost analyses, thus making the choice of targets vital.
Personnel
Some tests, such as enzyme assays, require a considerable amount of expertise to ensure reliable performance. The background of lab personnel needs consideration because understanding the science behind a test is sometimes necessary. Other aspects include the availability of training, mechanisms for staying current and the turnover rate of the lab. It is ideal when multiple people are trained for each assay, but this requires dedicating time that is outside of release testing. Even with an exemplary training program, turnover can cause a dilution effect that results in the ultimate failure of a lab to reliably perform a specific test. This is true for both in-house and contract labs unless due care is taken.
Equipment
Current in-house equipment with available capacity should be examined for other potential uses. For example, a gas chromatography system with multiple detectors and inlets has the capability of performing multiple methods (e.g., residual solvents and fatty acids), although not in the same run. For new equipment, attention to purchase price, qualification, operating costs and maintenance is a must.
Build-out
New lab equipment that requires special resources or operating conditions will necessitate a build-out. Those who neglect to include this component on a capital expenditure budget are sure to face the ire of the chief financial officer (CFO). Seeking guidance from instrument manufacturers in advance is highly recommended. Measuring twice is sound advice for general carpentry; imagine finding that a US$300,000 instrument will not fit into the door of the lab only after it has been delivered.
Method Development
Broadly speaking, tests with readily available, fit-for-purpose methodology take precedence over those requiring development from scratch. Many methods are somewhere in between these extremes, and it is common for adjustments to occur for even well-established methods when complex matrices are involved. In-house development of matrix-specific instructions can be a significant benefit if done correctly. Another example of potential in-house superiority is when a specialized coating on a dietary ingredient requires a unique extraction method that contract labs are unwilling to perform. Work with the ingredient manufacturer in this case, since that is where the expertise is.
Many other requirements must be considered, including the method verification/validation, standards, SOPs, and OOS investigations.
Ultimately, a quick, ballpark comparison can be performed as follows. Multiply the frequency a test is performed per year by the contract lab cost of a single assay. If this is greater than the cost of equipment needed for the test, prioritize the test for further analysis. Determine the criteria that are most relevant to your company and in-house lab. Give those a higher weighting when considering the potential for bringing a test in-house.
Michael Hoard, Ph.D., is the vice president of technical affairs for Arizona Nutritional Supplements (ANS). He received his doctorate from the University of Southern Mississippi and completed 14 years of post-doctoral work in natural products chemistry at the Cancer Research Institute at Arizona State University. He joined ANS in 2006, where he has concentrated on operations, regulations, test methods and audits related to the laboratory services department.
Learn more about contract labs from Michael Hoard, Ph.D., during the “Effectively Partnering with a Contract Laboratory” workshop on Wednesday, Nov. 7 at 1:30 p.m. at SupplySide West in Las Vegas.
About the Author(s)
You May Also Like