Developing a nutraceutical tablet means more than just considering the active ingredients and even excipients; understanding how the design of the tablet will impact production and delivery of the final product is critical to cost effective manufacturing and market success.
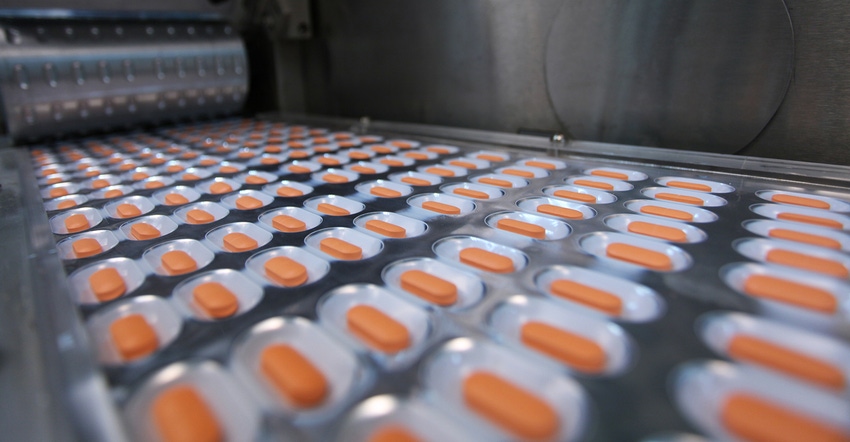
When it comes to successful tablet production, finished product design is fundamental. If this is not correct, problems down the line can be substantial.
Ingredients in nutraceuticals can be unrefined, abrasive, corrosive and particularly hard. This combination results in extensive wear and damage to the tablet punches and dies used during compression. It is therefore important to look at all aspects of the tablet design to ensure it is robust enough to withstand the rigors of ingredient compaction.
There are many areas in tablet design that should be considered at the earliest stage possible.
Keep in shape
One of the most critical elements to successful tablet production is making sure the tablet shape will work. Correct tablet shape is vital in achieving a quality end product that can be easily manufactured. The tablet shape and any markings are often utilized for brand identity and marketing, such as using an unusual shape like a robot to identify children’s vitamins or through elaborate embossing of a brand logo. This presents a challenge for the tooling designers who must incorporate the marketer’s demands and take into consideration a design that is robust and producible.
Speaking generally, tablets come in two base shape categories, round and non-round. Non-round shapes can vary in complexity and design and may require specialized tool manufacturing capability. Selecting the wrong shape (or a shape that has been badly designed) can have a huge impact on the bottom-line as problems like sticking and picking can ensue delaying production.
The ingredient mix will also affect the shape of a nutraceutical tablet. Often, these formulations have a high active to excipient ingredient ratio. The higher number of active ingredients brings challenges related to particle size, flow, compressibility, moisture sensitivity, ingredient interaction, content uniformity and quality control (QC) testing. For example, some active ingredients may be available in granular form, while some may be available only in fine powder form. Because of this, the ingredient blend may have many different particle sizes and ingredients with a variety of characteristics. This variation demands the shape and profile to be correct during manufacture.
Maintain a high profile in design
When a workable shape has been determined, the next consideration should be the tablet’s profile. This will be influenced by many factors including the granule, embossing requirements, coating process, packaging, swallowability, functionality and branding.
If a tablet design specifies the profile to have a deep curve, it can very often cause wear on the areas of tooling with the steepest gradient. The action of compression grinds on the punch tip face, removing material over time, which can lead to problems like delamination, when the tablet splits apart. This is particularly apparent with nutraceuticals due to the coarse structure of the ingredient, which brings with it excessive abrasion. However, there are tablet design features that expert tooling manufacturers can devise that help to reduce the effects of abrasion. By designing in a flatter tablet profile—perhaps adding a double radius—formulators can help to reduce the frictional action of the granule across the punch surface.
Another “trick” in the design book when it comes to abrasive formulas is to ensure the tolerance between the punch tip outer diameter and the die bore is appropriate to the formulation being compressed. Fine granules can infiltrate into this clearance, accelerating wear. When the granule is compressed between the punch tip and die bore, these surfaces can wear significantly, resulting in ringing, clawing and crowning of the punch tip. Having the correct tablet design, profile and clearance can help with this issue.
Don’t skim the surface
Adding a coating to a tablet can help with many factors: swallowability, physical and chemical protection, control of the release profile, and masking strong and unpleasant flavors and odors commonly found with ingredients such as fish oil or garlic.
Successful coating is largely dependent on the tablet profile. Coated tablets present challenges for the tablet designer as it is complex and requires expert help.
One of the most common problems is core erosion of the tablet during the coating process. Coating should be uniform and should not crack under stress. Generally, the coating solution is sprayed onto the uncoated tablets as the tablets are being agitated in a pan, fluid bed, etc. As the solution is applied, a thin film is formed, which sticks to each tablet. The liquid portion of the coating solution is then evaporated by passing air over the surface of the tumbling pans. The coating may be formed either by a single application or developed in layers through multiple spraying cycles. This puts stress on the core, as it needs to withstand the harsh process.
The center of a tablet is usually lower in hardness, which makes it vulnerable to the mechanical stresses and abrasion of the coating process. This problem can be overcome by understanding the procedure and applying measures during the design stage. These could include avoiding deep concaves or, in the case of film-coated tablets, adding a double radius profile to achieve successful coating.
For shallow tablets with hard, sharp edges, some coating processes have the potential to damage the exposed edge of the tablet, resulting in chipped edges and sometimes cracks. Therefore, flat and shallow tablet profiles should be avoided. Double radius designs ensure a robust tablet edge and a balanced profile, which will roll in the coating pan.
Seek advice for increased productivity
These are just three factors that can have a huge impact on tablet manufacture, but there are many others to consider from the tooling material and coating, to blended lands and branding. Getting the tablet design correct is crucial and should not be underestimated. Consulting with an expert tablet designer as early in the process as possible, can ensure that the tablet design is robust and producible in a rigorous nutraceutical manufacturing environment.
Alex Bunting is the marketing manager at iHolland.
About the Author(s)
You May Also Like